In today’s fast-paced industrial world, precision, flexibility, and customization are key to successful manufacturing. Whether you are in the automotive, medical, electronics, or consumer goods sector, having the right components is crucial to your products’ performance and reliability. Plastic Injection Molding, a leading custom injection molding parts manufacturer, provides tailored solutions designed to meet the specific requirements of diverse industries.
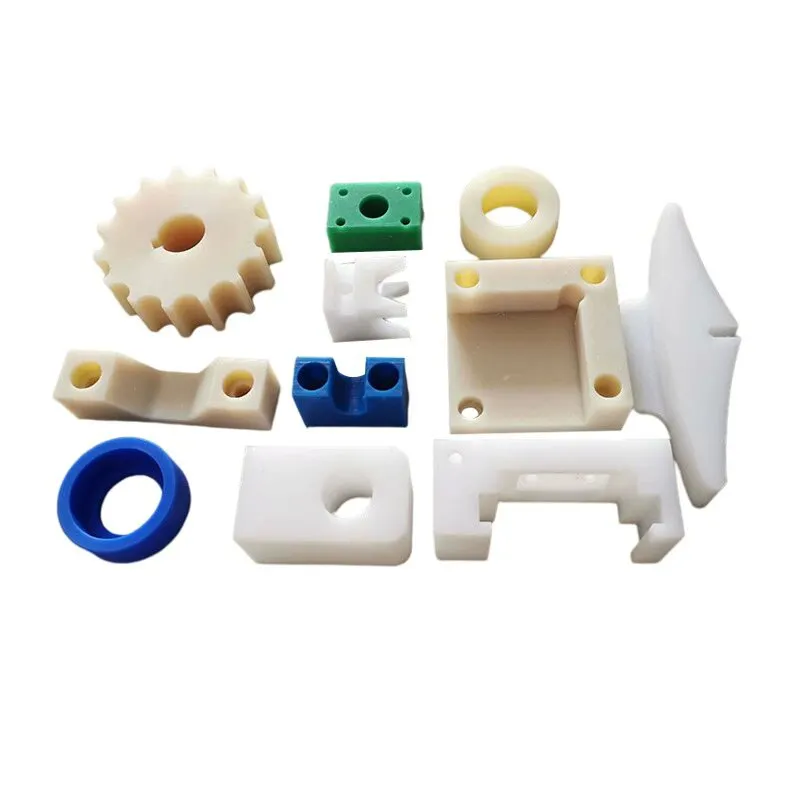
With our extensive experience and cutting-edge technology, we specialize in delivering high-quality, precision-engineered parts through our advanced injection molding process. Our focus is on helping clients streamline production, reduce costs, and improve product quality, all while maintaining the highest standards of craftsmanship.
What is Custom Injection Molding?
Injection molding is one of the most widely used manufacturing processes for creating plastic parts. It involves injecting molten plastic into a mold cavity, where it cools and hardens into the desired shape. Custom injection molding allows manufacturers to create highly precise, complex parts in a variety of sizes and shapes. This method is particularly beneficial when producing large quantities of parts with consistent quality and tight tolerances.
Why Choose Plastic Injection Molding for Custom Injection Molding?
At Plastic Injection Molding, we understand that every industry has its own unique requirements, and standard solutions often don’t meet the demand. That’s why we offer custom injection molding services tailored to the specific needs of each client. Here’s why you should choose Plastic Injection Molding for your next project:
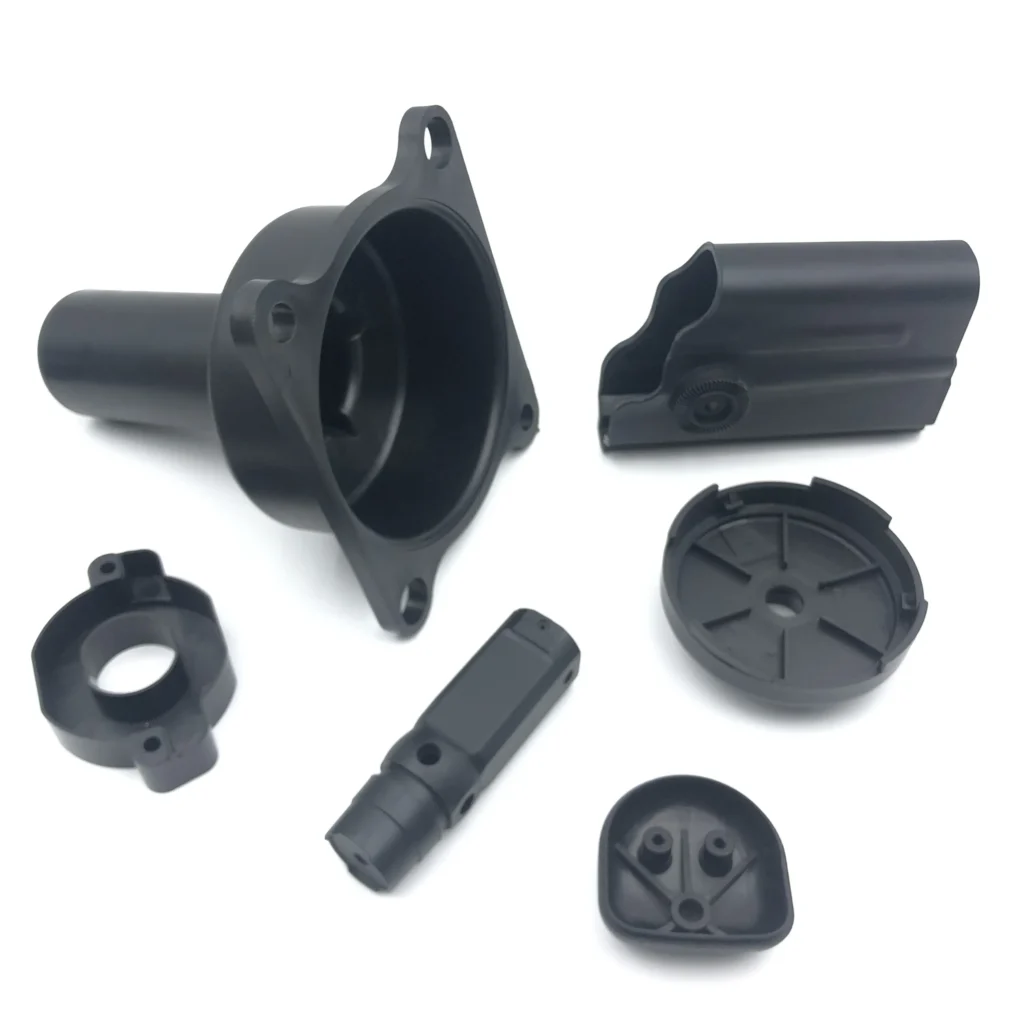
1. Expertise Across Multiple Industries
Our vast experience spans across a variety of industries, including:
- Automotive: We produce injection-molded parts for the automotive industry, including engine components, interior trim, and under-the-hood applications. Our high-performance materials ensure durability, heat resistance, and long-lasting quality.
- Medical: Precision and cleanliness are paramount in the medical industry. We manufacture medical-grade plastic parts with biocompatible materials, meeting strict industry standards for safety and performance.
- Consumer Goods: From electronics housings to everyday items, we provide custom injection molding for consumer goods, ensuring a balance between aesthetics, durability, and cost-effectiveness.
- Aerospace: For the aerospace industry, we produce lightweight, high-strength components that can withstand extreme environmental conditions, offering superior performance and reliability.
- Electronics: We manufacture intricate plastic parts used in electronic devices, from connectors and housings to small internal components, all with precision and reliability.
2. Advanced Injection Molding Technology
At Plastic Injection Molding, we use state-of-the-art machinery for our injection molding processes. Our facilities are equipped with:
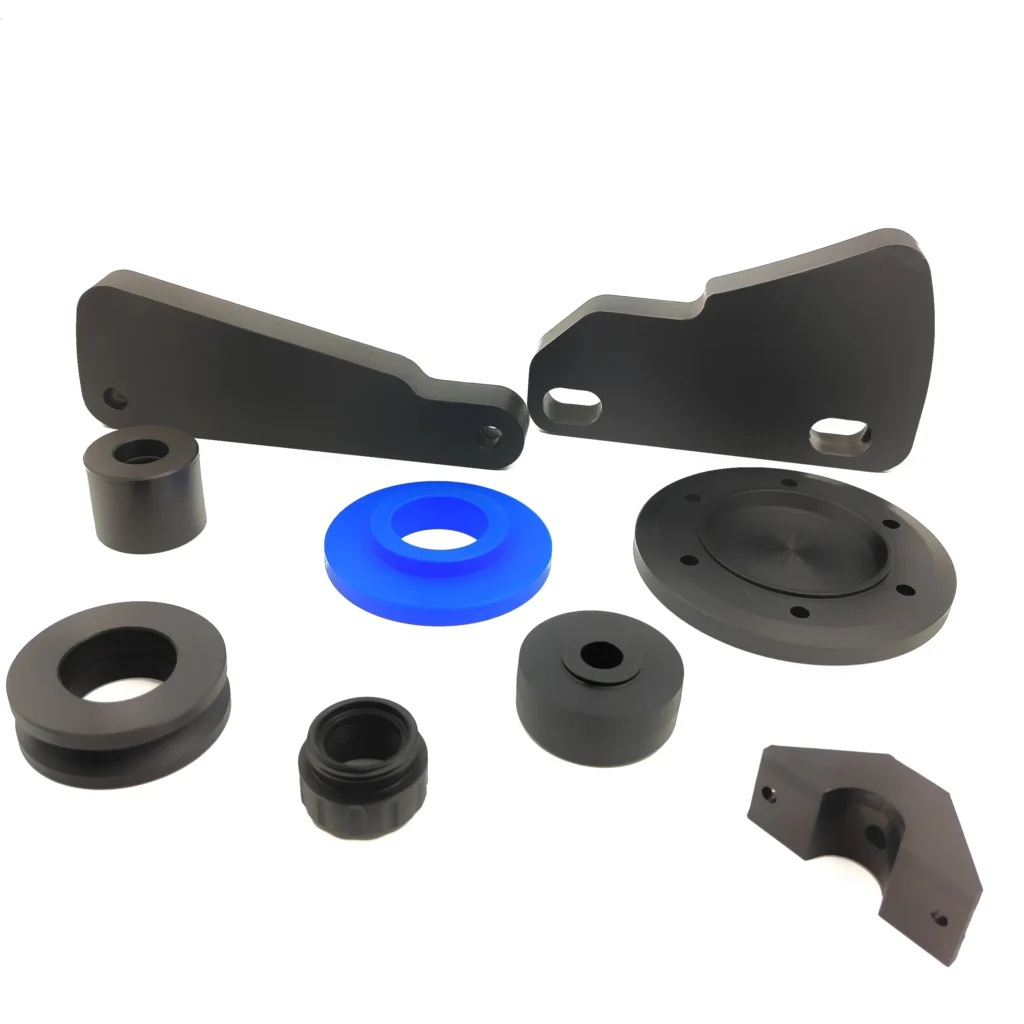
- Automated precision molding machines that can handle complex parts with tight tolerances.
- Multi-material molding capabilities allow for the integration of different materials in a single part.
- High-volume production: Whether you need a small batch or large-scale production, we can meet your quantity demands efficiently while maintaining consistent quality.
- Rapid prototyping: Our fast turnaround times for prototypes ensure that you can test and refine your designs quickly, leading to faster product development cycles.
3. Customization and Material Expertise
One of the major advantages of working with Plastic Injection Molding is our ability to customize each project to meet your exact specifications. From the initial design phase to the final production run, we collaborate closely with clients to ensure that every part fits their needs perfectly.
We also offer a wide range of high-performance materials to choose from, including:
- PEEK (Polyether Ether Ketone): Known for its strength, heat resistance, and chemical stability, PEEK is ideal for high-performance parts in demanding environments.
- Nylon: A durable material commonly used in the automotive and industrial sectors due to its wear resistance and strength.
- ABS: Lightweight and impact-resistant, ABS is perfect for electronic enclosures and automotive parts.
- Polycarbonate: This tough, transparent plastic is frequently used for protective housings and lenses.
- PVC, PP, PE: Flexible materials ideal for applications requiring chemical resistance and durability.
4. Quality Control and Assurance
We know that quality is non-negotiable. At Plastic Injection Molding, we have implemented a rigorous quality control process to ensure that every part we manufacture meets or exceeds industry standards. Our quality assurance process includes:
- In-depth inspections: We perform dimensional and visual inspections at every stage of production to ensure that each part matches your design specifications.
- Material testing: We test the physical properties of the materials we use to ensure they meet the requirements for strength, durability, and performance.
- ISO Certification: We adhere to ISO standards and maintain certifications that guarantee compliance with international quality and safety standards.
5. Cost-Effective Solutions
At Plastic Injection Molding, we understand the importance of keeping costs in check while delivering high-quality parts. By utilizing lean manufacturing processes and efficient production techniques, we help our clients reduce waste, lower costs, and improve overall productivity.
Our custom injection molding services are designed to deliver the best possible results while maintaining a competitive price point. Whether you’re a start-up looking for small production runs or a large-scale manufacturer needing high-volume output, we tailor our services to suit your budget and requirements.
Applications of Custom Injection Molding Across Industries
Our custom injection-molded parts are used in a wide range of applications, including:
- Automotive: Engine components, air vents, interior trim, and electronic housings.
- Medical Devices: Surgical instruments, drug delivery systems, and diagnostic equipment.
- Consumer Electronics: Phone cases, connectors, and circuit board housings.
- Aerospace: Lightweight brackets, clips, and fasteners.
- Industrial Machinery: Gears, bearings, and mechanical components.
Why Partner with Plastic Injection Molding?
With years of experience in the field of injection molding, Plastic Injection Molding is recognized as a leader in producing custom plastic parts for a wide variety of industries. We are committed to providing:
- Tailored solutions to meet the exact needs of each project.
- State-of-the-art technology to ensure precision and quality.
- High-performance materials to deliver durable, long-lasting components.
- Cost-effective manufacturing that doesn’t compromise on quality.
When you choose Plastic Injection Molding, you’re choosing a partner dedicated to helping your business succeed through reliable, customized injection molding solutions.
Get in Touch with Plastic Injection Molding Today
If you’re looking for a reliable partner for custom injection molding, look no further than Plastic Injection Molding. Our team of experts is ready to work with you to deliver the perfect solution for your industry. Contact us today to discuss your project and learn how we can help bring your ideas to life.